Resource
Maximizing OEE in a Connected Factory
Maximizing OEE in a Connected Factory
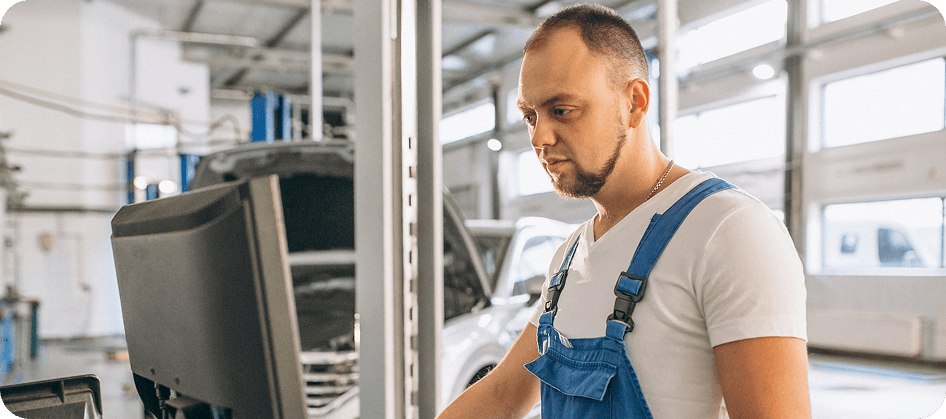
Predictive maintenance is transforming modern manufacturing by reducing unplanned downtime, minimizing material waste, and improving operational efficiency. By using real-time data and intelligent analytics, companies can predict equipment failures before they happen — preventing costly disruptions and scrap.
Key Benefits
✅ 1. Reduced Downtime Traditional maintenance is either reactive or scheduled — both can miss early failure signs. Predictive maintenance uses sensors and AI to detect anomalies in real time, helping teams: Replace parts before they break Schedule maintenance during planned stops Avoid production line halts due to machine failure
♻️ 2. Less Scrap and Rework Faulty equipment often leads to incorrect cuts, poor finishing, or misaligned components. Predictive systems ensure: Calibration alerts when precision drifts Real-time feedback on equipment performance Early intervention to maintain product quality
💰 3. Lower Maintenance Costs While predictive systems may require upfront investment, they often lead to: Fewer emergency repairs Extended machine lifespan Optimized use of spare parts and resources