Blog
Maximizing OEE in a Connected Factory
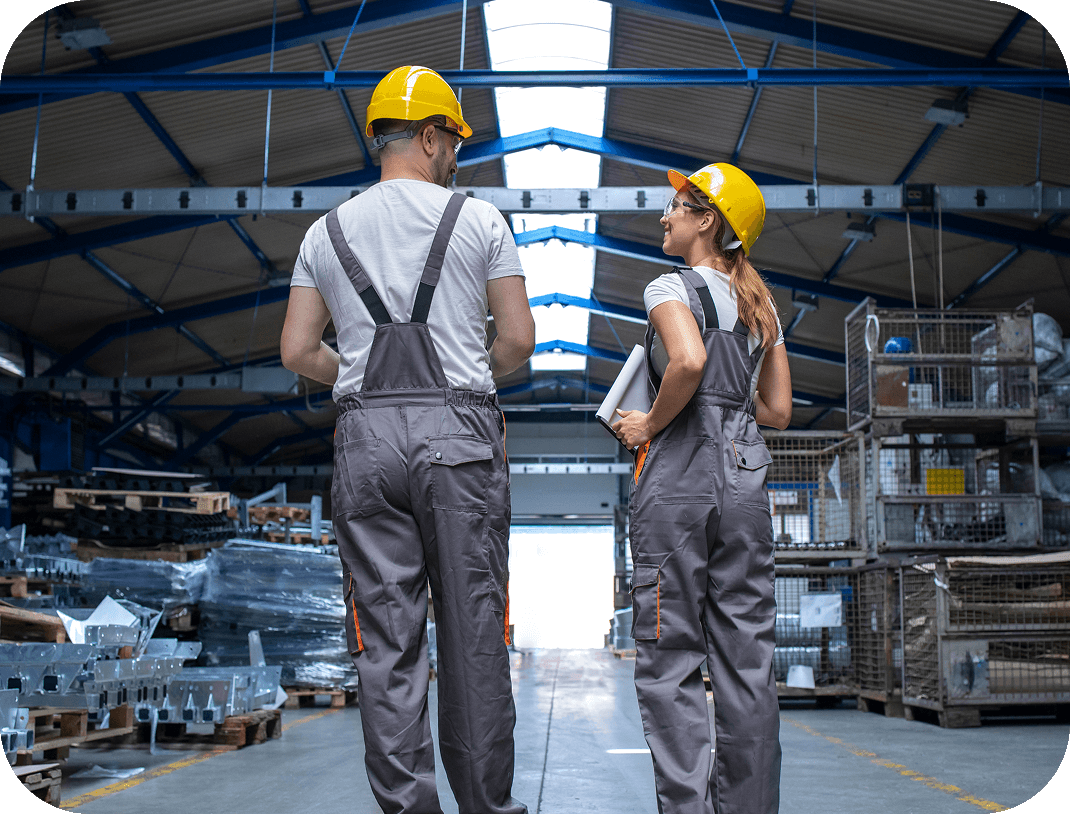
In the era of Industry 4.0, manufacturers are under increasing pressure to improve productivity, reduce waste, and boost profitability. At the heart of these efforts lies Overall Equipment Effectiveness (OEE), a powerful metric that quantifies how effectively a manufacturing operation is utilized. In a connected factory—where machines, sensors, and systems communicate seamlessly—maximizing OEE becomes not just a goal, but a continuous process enabled by data and digital intelligence.
Understanding OEE: The Foundation of Manufacturing Excellence
OEE measures the percentage of manufacturing time that is truly productive, combining three core factors: Availability (uptime), Performance (speed), and Quality (good output). An OEE score of 100% means perfect production: only good parts, as fast as possible, with zero downtime. World-class manufacturers typically target OEE scores of 85% or higher, but many factories operate well below this benchmark, leaving significant room for improvement.
The Role of Connectivity and IIoT
The Industrial Internet of Things (IIoT) transforms traditional factories into connected, data-driven environments. By deploying smart sensors and integrating equipment with cloud-based platforms, manufacturers can collect real-time data on machine status, production rates, and quality metrics. This connectivity eliminates the delays and errors of manual data collection, providing instant visibility into every aspect of production.
Automated data collection and reporting not only save time but also ensure that no critical information slips through the cracks. Operators and managers can access live OEE dashboards, historical trends, and actionable insights, empowering them to make informed decisions and respond quickly to emerging issues.
Tackling the Six Big Losses
To maximize OEE, it’s essential to address the “Six Big Losses” that undermine manufacturing performance: breakdowns, changeovers, idling, reduced speed, quality defects, and start-up losses. In a connected factory, IIoT systems monitor these losses in real time, enabling rapid root-cause analysis and targeted interventions.
For example:
-
Breakdowns: Predictive maintenance, powered by real-time sensor data, helps identify potential failures before they cause unplanned downtime.
-
Changeovers: Automated scheduling and data-driven workflows streamline transitions, reducing planned stops.
-
Quality Defects: Continuous monitoring of process parameters enables early detection of deviations, minimizing scrap and rework.
Leveraging Data for Continuous Improvement
The true power of a connected factory lies in its ability to synthesize data from multiple sources—machines, MES, ERP, and maintenance systems—into a unified view of operations. By analyzing OEE data alongside maintenance records and quality reports, manufacturers can uncover patterns, identify bottlenecks, and prioritize improvement efforts.
Techniques like Pareto analysis help teams focus on the factors that have the greatest impact on OEE, ensuring that resources are allocated where they will deliver the most value. Continuous improvement methodologies such as Lean Manufacturing and Six Sigma further enhance OEE by eliminating waste, reducing variability, and optimizing workflows.
Real-Time Accountability and Collaboration
Connected factories foster a culture of transparency and accountability. When operators and managers have instant access to OEE metrics and production reports, they can quickly identify underperforming assets, share knowledge across shifts, and collaborate on solutions5. This visibility not only drives immediate improvements but also supports long-term cultural change toward operational excellence.
The IoTiView Advantage
Platforms like IoTiView empower manufacturers to maximize OEE by providing end-to-end visibility, automated data collection, and advanced analytics. With seamless integration across legacy and modern equipment, IoTiView’s solutions help factories of all sizes unlock the full potential of their assets—without costly overhauls.
Conclusion
Maximizing OEE in a connected factory is a journey, not a destination. By leveraging IIoT technologies, real-time data, and proven improvement methodologies, manufacturers can drive sustained gains in productivity, quality, and profitability. The connected factory isn’t just the future—it’s the new standard for manufacturing success.
Ready to boost your OEE? Discover how IoTiView can help your facility achieve world-class performance through connectivity and data-driven insights.